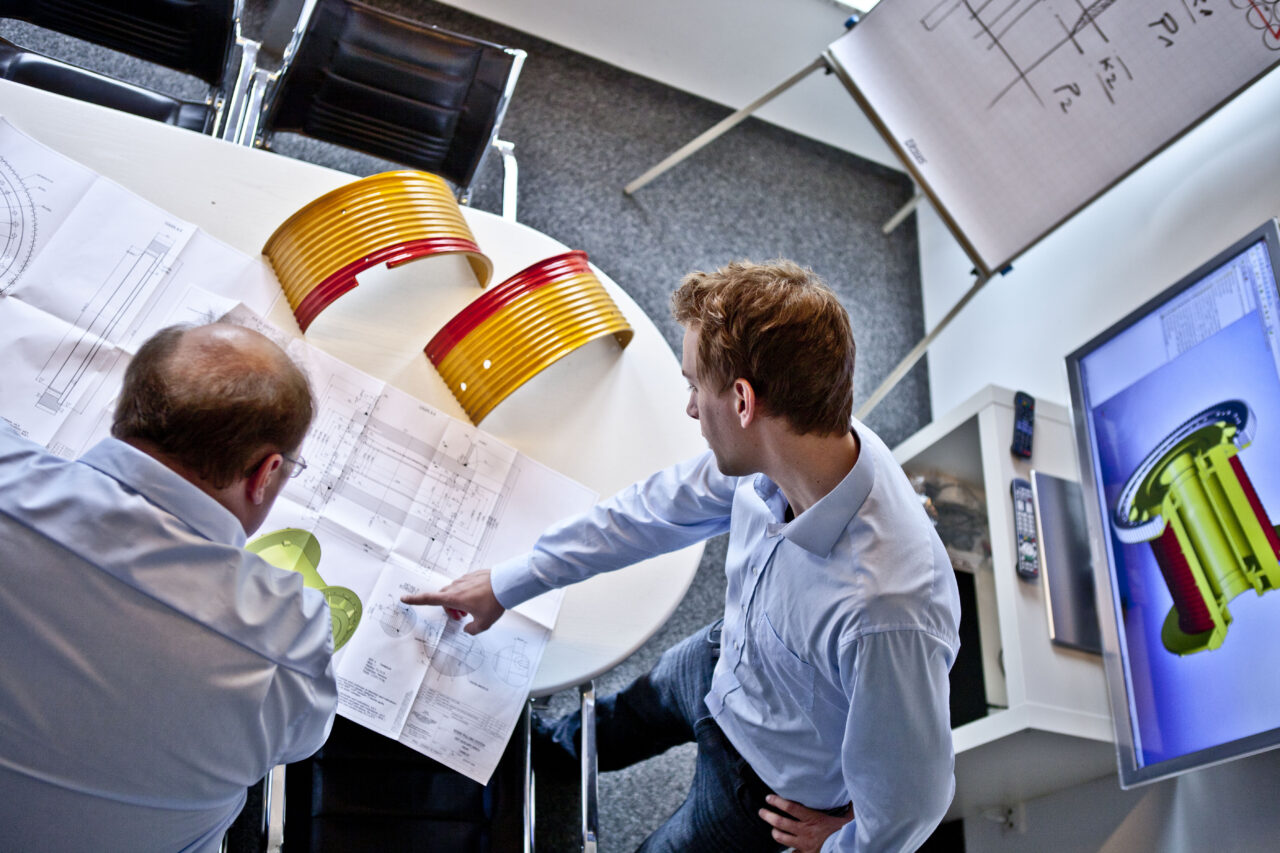
How can we help?
Advice on all aspects of the LEBUS® system
We value personal consultation. Through direct discussions, we find solutions and develop new ideas tailored to your specific application. However, some questions come up frequently. That’s why we have compiled a selection of common inquiries—our FAQs. Is your specific question not covered? Feel free to contact our experts in Finning am Ammersee.
Contact usEnough reading.
Would you like to speak to our engineers directly?